Case Study – La Fromagerie Gourmande de Montricher

Towards greater efficiency and sustainability
Thanks to the implementation of a monitoring and optimization system at La Fromagerie de Montricher, the world’s largest producer of Gruyère PDO has considerably reduced the costs and environmental impact of its production and overall activities.

1
dashboard
with accessible, demystified data
16’000 CHF
annual savings and reduction of 15 kg of CO2/year
30%
30 %
reduction in peak electricity bills
Context
The facility with its 5 sectors of activity
Production
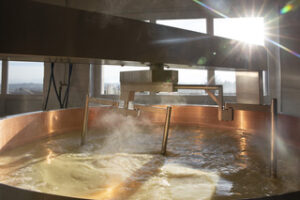
Cellar
Â
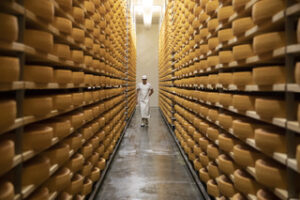
Store

Exhibition

Restaurant

Challenge
The facility uses a significant amount of electricity with approx. 210,000 kWh or 36,000CHF/year.
Without any optimization, the drastic price increase in 2024 (from 17 cts/kWh to 33 cts/kWh) would double costs to approx. 70’000 CHF/year.
It is important to accurately measure the distribution of this consumption with a view to more efficient management.
The challenge is to implement energy monitoring with a dual objective:

Cost reduction

Reducing environmental impact
Solution
The installation implemented by ICUBE
Upstream preparation
Analysis of the electrical topology of the cheese factory’s production machines. The main current outlets are identified: motors, ventilation and air conditioning, chilled water production, heat production, sockets and lights, etc…
1-day installation
The data acquisition box is quickly deployed on site. Its accuracy is far superior to that of standard electricity meters.
Remote check
Thanks to a secure connection, analysis is carried out remotely by our experts, without any on-site intervention.
Dashboard
Instant transmission of all power and energy data to an online dashboard
Analysis
After the first few days of acquisition, it is already possible to carry out analyses to draw the first correlations between consumption peaks and appliances in operation: optimization can begin!
Improvements & Results

A dashboard with accessible, demystified data. Thanks to instant and precise information on consumption, optimization is possible and employees can quickly get involved in the process.

Separation of production and warehouse chillers to prevent accidental start-up.
Results: CHF 16,000 in annual savings and reduction of 15 kg of CO2/year

Installation of inverters on certain motors. Gradual, staggered motor ramp-up reduces power peaks.
Results: 30% reduction in peak electricity bills

The installation of solar panels will enable very interesting self-consumption, as the cheese dairy’s production equipment can be partly modelled on solar production.
Other possible improvements :
- Regulation of cooling and heating production.
- Regulate compressor flow and compressed air use. Advantage: reduced network flow when there is no production.
- Adapting habits to solar production.
- Consider sizing and insulating energy storage (heat, cold, compressed air, electricity). Ideally, this should be considered at the construction stage.
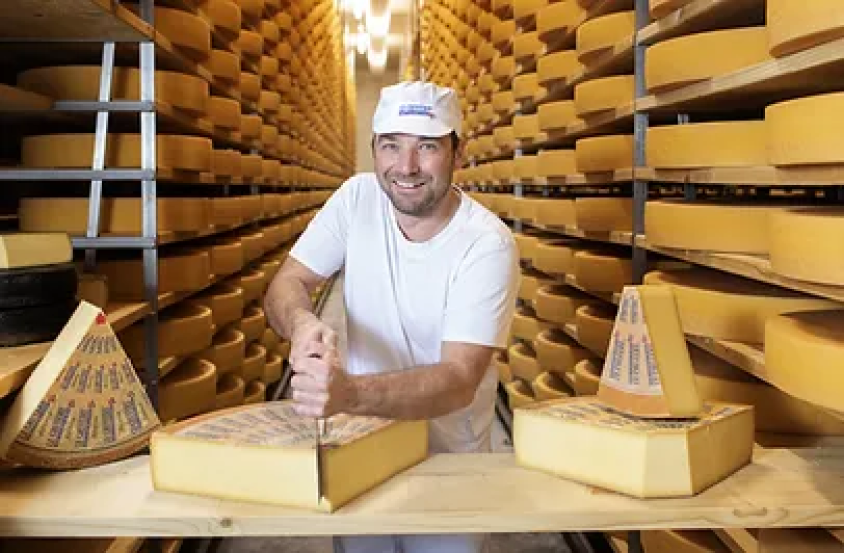
“
“I contacted ICUBE to be able to analyze my energy consumption sector by sector, in order to optimize self-consumption. They took care of everything from A to Z, and returned the relevant information live in EVA. This precise vision and ICUBE’s advice revealed significant and unsuspected wastage, which could be remedied by obvious improvements.
I’d like to thank ICUBE for their attentiveness and expertise, which made this possible!”
Etienne Aebischer
Managing Director, La fromagerie Gourmande
Like La Fromagerie Gourmande, opt for an ICUBE solution tailored to your production line.
Summary
- Improving energy consumption is essential
- To improve, we must above all: measure
- The installation of the electricity measurement sensors was carried out rapidly thanks to the measurement and analysis system developed by ICUBEÂ : EVA
- Continuous comparison of power consumption with production tool usage enables manufacturing to be optimized.
Schedule an appointment with our teams today to discover a customized, efficient solution.